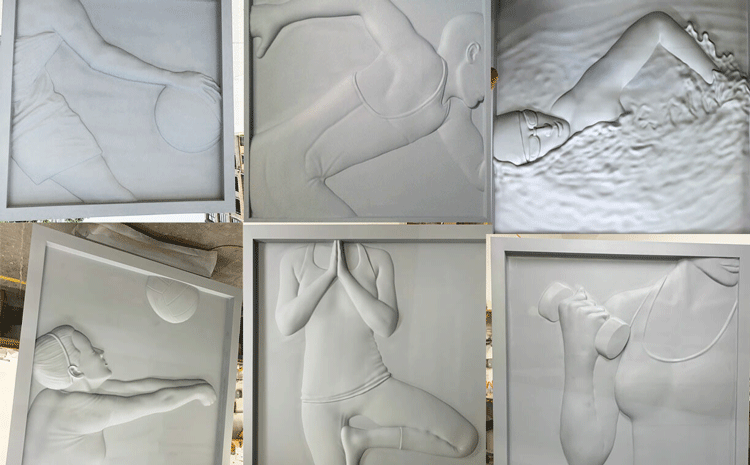
HUB Medallions: A Freeze-Frame of Athletes in Motion
Oct 25, 2019
The idea of bas-relief sculptures capturing a freeze-frame of athletes in motion came naturally to Mike Schuster about two years ago when he was considering what should be installed as a decorative element for the outside of Xavier’s new five-story Health United Building.
The process for converting his idea into reality, however, was a whole different story. Schuster, president of MSA Design architects and a long-time sports fan, Xavier supporter and coach of boys’ select baseball, did not know how difficult it would be to bring his idea to fruition. But that didn’t matter because once Schuster latched onto the idea, there was no turning back.
“The vision was to convey what is going on inside the center, and because we were using stone, we started working with the idea of bas-relief,” he said.
He wanted something traditional, something reminiscent of the ancient Roman bas-relief marble sculptures of wrestlers and charioteers to break up the monotony of the brick facade and provide a bit of artistic inspiration at the same time. The large medallions would convey the essence of human sport, focusing not so much on the athlete as the athleticism—the swimmer’s arm in water, the hand on the basketball, the runner’s crouch. The medallions, he mused, would also remind us of the sculptures of athletes on the walls of the old Cincinnati Gardens, where Xavier’s early glory days of men’s basketball once flourished.
“The medallions I thought fit the bill for the inset where windows might be, and as people walk along and see the medallions, they would see the movement in basketball and swimming, so in a subtle way it tells the story that it is a fitness and recreation center,” Schuster said.
But what is normally a simple process of hiring a concrete company to create a decorative sculpture that then hangs on a wall turned into a multi-step process involving five companies in three states and lasting 32 months. The scope of the project and the intricateness of the sculptures required the skills of a professional 3D digital sculptor and a special late-model sculpting machine.
The process got started in early 2017 and by October of 2019, 13 concrete medallions, each measuring 6 feet 8 inches square and weighing 2,100 pounds, were on site at Xavier, ready to be hoisted and set into place around the upper brick sections of the new Recreation Center. It is part of the Health United Building, where a unique combination of academic classes, athletic activity and health services are provided under one roof.
Each step of the process had to be performed with meticulous precision in order to provide the foundation for the next, so each sculpture could emerge a perfectly completed execution of Schuster’s idea of athleticism in motion. It is, he hopes, a permanent reminder that Xavier is as much about health and wellness as it is about academic achievement.
THE IMAGES
The first step was to select the images. Schuster’s team of designers settled on black and white images of a basketball player, a swimmer, a weight-lifter, a volleyball player, a runner and a yogi. Each would be made into two medallions and one, the basketball player, would be made into three.
“We thought it evoked the whole idea of the Roman coliseum style of carved sculpture of stone with an athletic bent to it as well as something that signifies athletic accomplishment,” said Brian Baker, project manager at MSA architects. “They were looking to represent what was going on inside the building, the health and wellness aspects, and they tried to bring in discreetly the angles of the X plus diversity of gender and age to show this is a space for all people, all types.”
THE ART
The architectural design team converted the black and white photographs into two-dimensional digital graphic images. But to convert them into three-dimensional models from which the sculptures could be created required the talents of a professional digital sculptor.
Enter Travis Barker. The Lakeland, Fla., artist does decorative work for the Bybee Stone company in Indiana, creating objects like finnials, flowers, angels and archways for projects at churches and universities. But this was different. Instead of limestone, this was pre-cast concrete, and instead of inanimate objects, these were sculptures of human forms.
Using a digital sculpting software program called ZBrush, Barker used the photos from MSA as a guide to recreate the image on a digital drawing tablet. With digital sculpting tools, Baker literally sculpted the forms on the tablet while viewing the image on a large monitor.
“ZBrush is so powerful because what I’m looking at looks like you could pick it up off the screen, and you can rotate as you sculpt, just go around it like you’re walking around it,” Barker said. “It’s different from what I’ve done in the past. This is the most modern piece I’ve done in bas-relief. I liked it because there is more anatomy involved.”
Each medallion took about a week to create, but the swimmer was the most challenging. Barker estimates it took over 70 hours to complete just that one form because of the intricacies of sculpting water and the back and forth for revisions and approvals. He studied YouTube videos of swimmers in slow motion and ended up building the image in layers.
“The main trick I used was to have enough ripples to make it display motion in water, but you don’t want any hard lines. It’s all about smoothness and depth. You want it to look fluid and still be 3-dimensional,” he said.
THE FOAM MODELS
Barker’s digital files of the completed 3D models were sent back to Cincinnati to be produced as life-sized models. Project managers at Messer Construction sent them to ANZA Inc. in Cincinnati which has a CNC machine that carves foam models from 3D images.
Each of Barker’s 3D images was broken into several segments because the whole medallions were too large to do in one piece. Anza loaded the files into the CNC machine and, one by one, created exact replicas of Barker’s sculpted images out of a dense foam call Renshape.
“The beauty of this is what was designed from start to finish is exact,” said Matt Mintus, a project solutions coordinator at Messer. “It’s a computerized cutting machine.”
THE MOLD
The Renshape forms were then sent to ReadingRock, a building manufacturing company north of Cincinnati, which made molds by pouring a silicone rubber-like substance over the forms. Once dried, the molds were removed from the forms and set into wooden frame boxes to hold them in place in preparation for the final pour of pre-cast concrete.
THE PRE-CAST POUR
Over the summer and fall, ReadingRock poured concrete into the 13 molds, one by one in succession, until the last one, the weight-lifter, was poured on a warm Friday morning in September. A team from Xavier looked on in the pouring bay and took video as a small work truck lifted a pouring bucket over the framed mold lying flat on a work table. Workers in orange shirts turned a wheel that moved the bucket’s pour spout back and forth across the mold, then turned and poured in the opposite direction. The wet gray concrete slowly filled the wooden frame.
The workers dragged a concrete rake across the surface to flatten it, then sawed a vibrating board back and forth over the top to shake the trapped air bubbles to the surface. They laid an iron rebar grid down into the wet concrete to give it strength and raked it smooth again. In 24 hours, it would be cured and ready for the final finishing process.
THE ACID WASH
The final step for all the medallions was the acid wash to clean the concrete surface. After the weight lifter had cured overnight, the ReadingRock team disassembled the wood frame and lifted the hardened medallion out by crane. They removed the silicone liner, set the medallion onto a pallet and sent it outside for a pressure wash to open the remaining "bug" holes for patching. Once dried, it went into a washing bay for the acid wash before going back outside to wait for the trip to Xavier, its slightly roughened tan surface reflecting just a bit of sparkle like a shiny sugar cube.
“To me the story is that you can take something digital into the real world and there’s not much deviation at all,” Mintus said. “The swimmer’s ripples are the same as what was created digitally. There is very little loss of fidelity from the 3D image to creating a positive model that then becomes the mold and final sculpture.”
By France Sloat, Office Marketing and Communications
Video by Cliff Jenkins, Office of Marketing and Communications
Basketball image by Greg Rust, Office of Marketing and Communications
Feature image courtesy of Travis Barker
View a video by Messer about the medallions project.